Plan your Supply Chain with Uncertainty
Planning is performed primarily to avoid risk as well as improve operational efficiency leading to higher gains in business and better customer satisfaction. Planning is not too hard until the uncertainty is considered as a norm, not an exception. Traditional planning techniques such as most current S&OP solutions are not capable of taking uncertainty into account and assume it is an exception that can be addressed when and if it occurs! In certain cases, they try to hedge with inventory that may not be necessary, adding to cost and inferior customer service. Moreover, the incentive is to be safe than sorry. People have a higher incentive to increase the inventory than face the problem of running short, whether it is needed or not.
Taking uncertainty into account while planning is a must, otherwise why bother. A simple spreadsheet gives you all the answers that you need when everything is assumed predictable. S&OP solutions do provide some level of “visibility.” For example, demand planning gives some visibility into your future demand, but on the supply side, how much visibility is possible unless one can deploy techniques that determine supply side uncertainty. Supply chain practitioners have always assumed demand side variability, but supply side remains mostly deterministic. Assumptions are made about supplier delivery lead-times, resource availability or transportation times that may have been valid years ago. However, the chances are that they have changed, and they vary depending on seasonality, quantity, region and quality amongst other factors.
What is Uncertainty?
Supply side uncertainty takes two different forms, internal and external. Internal uncertainty has to do with how the digital twin, or the digital model, of the supply chain behaves. As described earlier, these are assumptions made about operational parameters such as manufacturing cycle times, supplier lead-times, transportation times in summer vs. winter, or even setup times and yield factors. On the other hand, external uncertainty has to do with how the suppliers and customers are impacted by disruptions such as labor strikes, fires, oil spills, airport shutdowns, earthquake regions and so on. Planning with uncertainty takes all such factors, both internal and external, into account.
No matter how good the plan is, there are always surprises and things happen for which we may or may not have accounted for. Thus, we need to plan with uncertainty and then be able to respond when we know with certainty a disruption is coming or has already occurred. An example would be a tornado in Florida. We can account for the possibility or likelihood of tornados at certain times of the year, but we also need to respond when we know it is coming with certainty a few days before or after. We may not have the same luxury of prior notice in case of (say) an earthquake in Taiwan. What makes the response challenging is that when it happens, the system ought to be able to respond immediately, in real-time. There is not much time for manual changes and a handful of scenario planning leading to inferior solutions.
Using Uncertainty to Have Superior Plans and Faster Response
Every time a system performs the planning function, there are many sources of information that can be used to evaluate the risk of the plan, depending on the objectives of the management. The risk may take different values depending on whether we are planning for profit, for resilience, for lower carbon usage, less dependency on a certain region or commodity, or all the above. A more reliable supplier nearby may offer a lot more reliability and higher resilience in delivering but at a higher price. The amount of risk we are prepared to take also depends on the customers. Certain customers may insist on on-time delivery but higher and repetitive purchases; some may have lower expectations but not as profitable. To this end, the system needs to understand the uncertainty of the supply side and the level of risk that is acceptable to the business as well as its customers.
The approach that we have taken is to consider both types of supply side uncertainty, internal and external, built into the plan using the available information and attributes of suppliers, regions, ESG factors etc. Thus, every time a plan is generated, for each customer or customer family, the risk in delivery is evaluated and the stochasticity of the supply is considered. Consequently, every plan is continuously refreshed based on current levels of uncertainty on the supply side. For example, if a supplier delivery is needed from Ohio, the plan may allow a little more extra time in winter than other times of the year based on the likelihood of snowstorms. A warehouse in Florida may be exposed to more risk of a tornado delivering goods in Fall than any other time.
Above describes plans that are produced based on the management objectives and likelihood of risk on the supply side. However, how do we respond when a disruption occurs, whether it was predicted or not? There are many companies that provide periodic information on a daily or weekly basis describing events all over the world in tens of different languages. Furthermore, they inform the subscribers of their services, specific occurrences of a disruption that has happened on the supply side or customer side. Other sources are weather stations and government/financial agencies that indicate risks in regions or financial exposure of suppliers. Examples are an airport strike where goods are being sent from, an oil spill preventing operations of a supplier for 3 days or reduced rating of financial viability of a supplier. To respond effectively and swiftly, the system can measure the relevance and impact of each event in real-time and make recommendations to the end users as to how to alter the plan. Given that there are hundreds of emails and messages coming to any given supply chain daily. A labor-intensive receipt of messages trying to respond to them manually is not a very practical and effective way. Therefore, automation of decision making, understanding the impact, and finding a good solution is essential.
Recent development of techniques such as Generative AI and machine learning, has paved the way to augment complex decision making and even autonomate the process by considering millions of variables and understanding their hidden relationships so that much better outcomes are made available to the supply chain leaders; or even new discoveries are made about the underlying causes of events and their impact on the supply chain. For more information on such developments click Here.
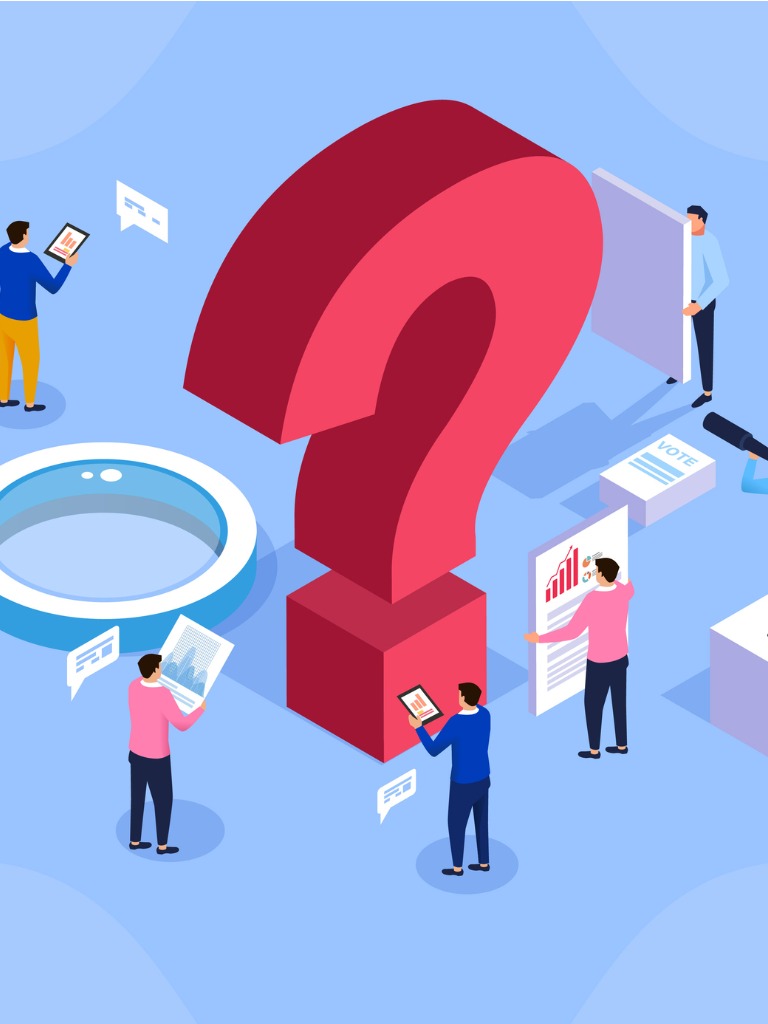